My big dilemma this weekend is what setting to use on the kiln to fire my PMC standard.
As you may recall, when I followed the “optimal” firing schedule for my first batch of PMC+ (1650 F for two hours), I killed the silver.
I took the other half of what I’d made (but hadn’t yet fired) and fired it at a lower temp (1110 F) for 45 minutes. Pretty drastic change, I know… but once you’ve obliterated half a package of silver metal clay, you become fairly cautious.
If the melting point of Bronze is 1743 and I fire at 1480, that means I’m firing at 263 degrees below the melting point. So if the melting point of fine silver is 1760, I should be able to fire at 1497.
But there’s another way to look at it. If I’m supposed to fire Bronze at 1540, then I’m dialing down by 60 degrees. With that reasoning, I’d want to fire my silver at 1590 (60 degrees below the normally recommended schedule).
I think maybe I’ll test fire a piece before putting my “goodies” in the kiln.
So I made a tiny little snake and put him in at 1590 F for two hours. Wish me luck!

Okay, the snake came out appearing fine. So fine, in fact, I didn’t have the heart to break him open and see if I can recognize a “sintered” versus a “not fully sintered” piece. I took the other thing I’d been working on—a piece of plastic from the throat guard of Monica’s helmet… that broke off when a hard shot came at her earlier this year… and she wanted to keep the piece rather than throw it away… so I filed it down and smoothed it out and drilled a hole in it. I put the snake on top of the plastic pendant and put both onto a sterling silver chain to be worn as a necklace.
I just realized I can’t fire my silver pendant because I need a smidge more clay to finish it and I don’t have a smidge. That will have to wait, then, until I pick up some more PMC Standard. As for the leaves… I drilled my holes (after making a quick decision whether they’d hang or be used as connectors) and stuck ‘em in the kiln.
A few hours later and they’re out. They don’t appear as white as the snake was. They actually seem rather dark gray (like that first, burnt batch), but they seem to have retained their shape. Next is cooling them, then rinsing and burnishing to see what I have.
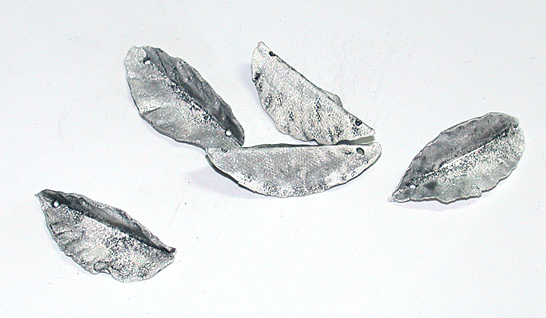
Then I took one leaf and burnished it.
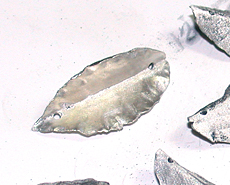
Then put a patina on it.
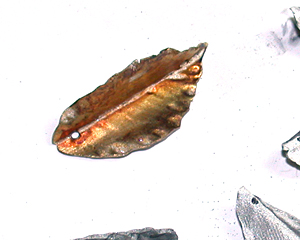
Then polished off most of the patina… but I have to clean up now and get ready to photograph ‘cause I have to go to Mon’s scrimmage at six and I’m going to swing by X-Sport first to get her a stick (she broke her only stick during last night’s practice).
Next steps are working on my peacock and putting together my silver leaf necklace.
I have a small set of charms to give away, too… just one Chinese pendant and two leaf charms that could be earrings.